Many carbon steel parts from Powerbrace Corporation are coated with zinc in a process to provide maximum protection from corrosion. Zinc can be applied to steel parts by electroplating, painting, or hot-dipping, also called galvanizing. Hot-dip galvanizing, where the part is dipped into a bath of molten zinc, provides the thickest coating.
Powerbrace Coats to an Extremely High Standard
Powerbrace follows the highest standards in galvanizing parts, because its products when mounted on trailers are in a highly corrosive environment. Corrosion occurs through exposure to moisture and salt. Any damp weather or precipitation provides moisture, and salt occurs on salted highways in winter and near any salt-water coastal area.
Powerbrace parts are coated per ASTM A 123 (Galvanized Steel Products) and ASTM A l 53 (line Coated Steel Hardware) standards. The average coating thicknesses for Powerbrace products are:
-
Hinges: 3.90 mil
-
Levers, Guide Plates, Seal Pins, Seal Plates: 2.21 mil
-
Lockrods: 3.00 mil
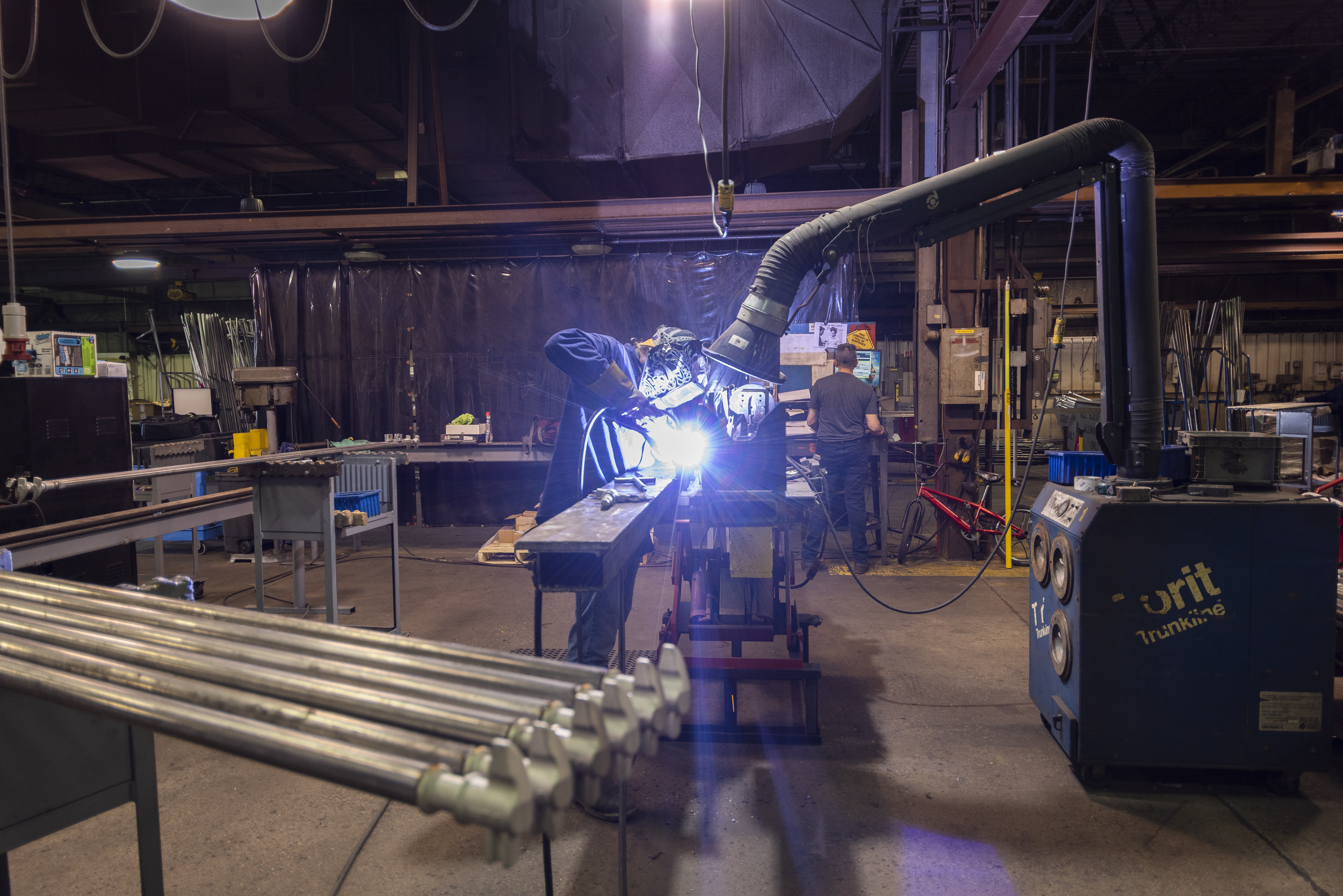
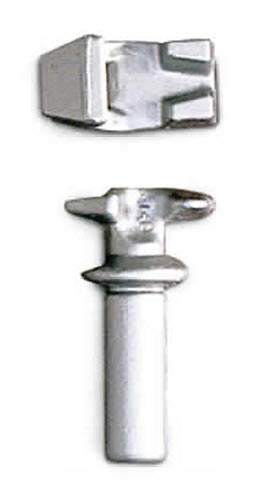
Other galvanized coatings are held to lesser standards. For example, a pre-galvanized G90 sheet trom steel suppliers has a coating of about 0.75 mil per side, significantly less than that of hot-dip galvanized steel. Commercial zinc has a coating of .2 to .5 mil.
A mil equals 0.001 ", or one thousandth of an inch. One rule of thumb in the industry (which is widely variable depending on weather exposure of the part) is that for every thousandth of an inch of zinc coating, the part resists corrosion to red rust for l O years. Thus, a hot-dip galvanized Powerbrace hinge with a 3.90 mil coating of zinc could last nearly 40 years, again depending on exposure to moisture and salt.
What is Corrosion?
Corrosion is an electrochemical process that occurs because of differences in electrical potential between dissimilar metals in contact in the presence of an electrolyte. Moisture and salt provide the electrolyte, allowing the flow of electrons from anode to cathode. Disintegration occurs in the anode metal.
Because zinc is above steel on a scale of active metals, the zinc will provide sacrificial protection to the metals below it Zinc therefore protects steel by sacrificing itself as the more anode metal, while the steel is protected, being the cathode metal.
Wet Storage Stain
Many users of galvanized steel will recognize a white or grayish stain on galvanized parts, especially when stored or shipped under damp and poorly ventilated conditions. This stain, also called white rust, is a result of the storage environment and is not a sign of inferior galvanized quality.
Typically the white stain will disappear with weathering. It usually does not indicate a weakness in the galvanized coating. Zinc is very reactive, so a zinc surface in contact with the surrounding air will form a film of zinc oxide. This thin, hard, tenacious film is corrosion-resistant and helps prolong the life of the part. The zinc oxide film is not able to form where air is not allowed to circulate.
When galvanized products are closely packed together without freely moving air, the zinc gets the white or gray wet storage stain because it cannot form the protective zinc oxide. Unless the product has been closely packed for very long periods of time, the wet storage stain will disappear when the part is exposed to air again, without any damage to the corrosion-resistant properties of the galvanizing.
Repair After Welding
When a galvanized part has been welded, the galvanized zinc coating has been compromised, allowing corrosive elements to attack unprotected steel. The weld area must be protected by restoring the corrosion resistance.
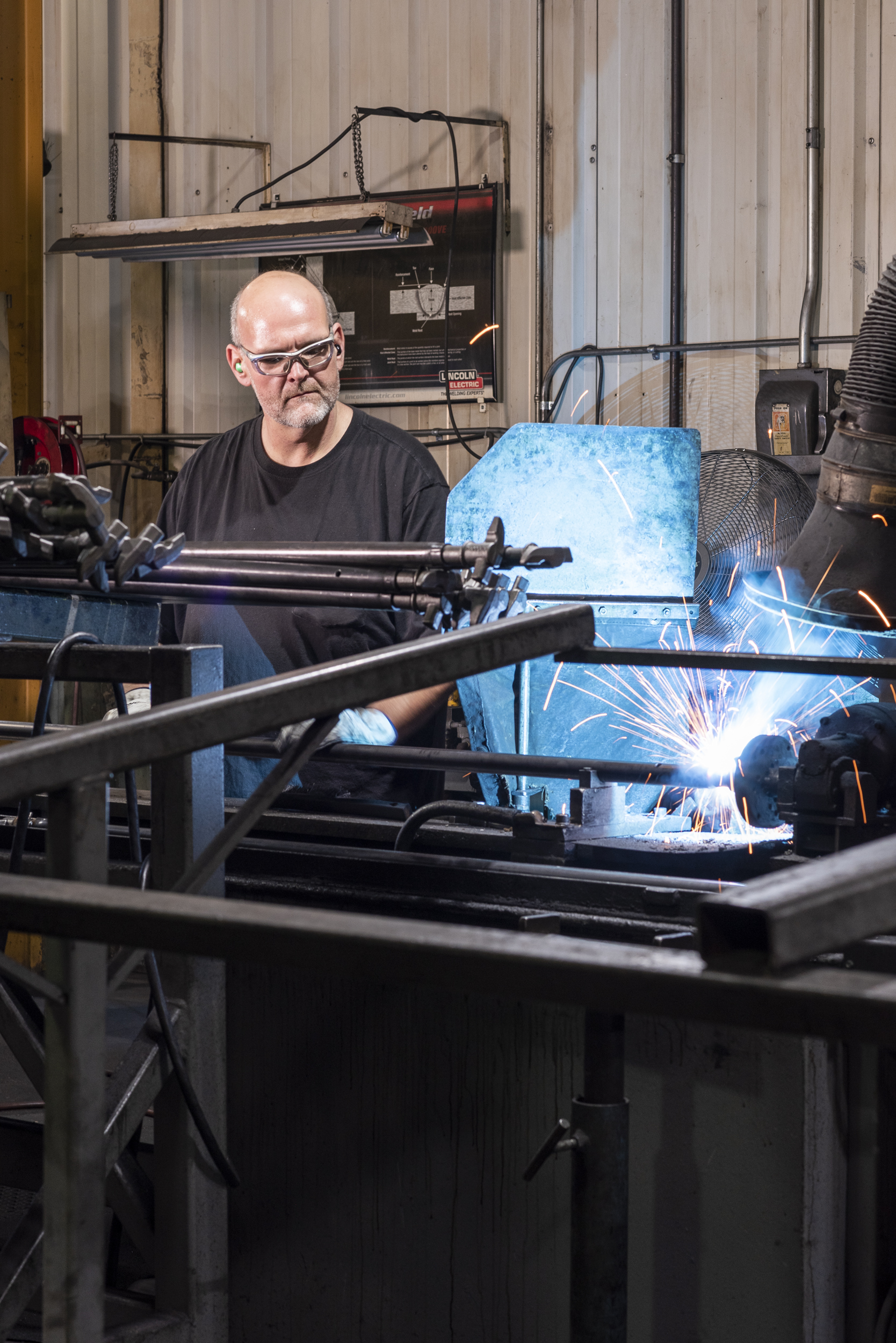